
Diecasting's process begins with the meticulous design and creation of molds, mostly made from steel hardened. These molds, referred to as dies are created by hand with the greatest precision, so that they reflect the intended final product. Whether it's intricate automotive parts or intricate electronic components dies are required to encapsulate each part with the utmost precision. The latest technologies, such as computer-aided designs (CAD) as well as computing numerical control (CNC) machining have revolutionized die production, enabling precise designs, while also reducing possible errors.
Moreover, die casting offers an exceptional versatility of materials, allowing the widest range of alloys and metals that can meet different requirements for applications. Zinc, aluminum and magnesium alloys are frequently used due to their superior mechanical properties, the light nature as well as their recyclability. Every material has its own unique attributes such as aluminum, which is prized due to its high strength-to-weight ratio and the resistance to corrosion, zinc due to the excellent stability of its dimensional properties, and magnesium for its exceptional hardness and stiffness. Its versatility allows companies to choose the most suitable material for their specific needs whether for automobile components and consumer electronics, or industrial machines.
Furthermore, diecasting permits the creation of complicated geometric shapes that are difficult or impossible to achieve using other manufacturing processes. Its ability to produce intricate designs with minimal adjustments to tools makes it the ideal option for the mass production of components featuring intricate details, for example, heat sinks housings, brackets and heat sinks. This capability not only enhances the design flexibility but additionally opens new avenues for innovative solutions across all sectors. From intricate designs on ornamental hardware, to the intricate cooling channels inside electronic enclosures. Diecasting enables designers to challenge the limits of the possibilities.
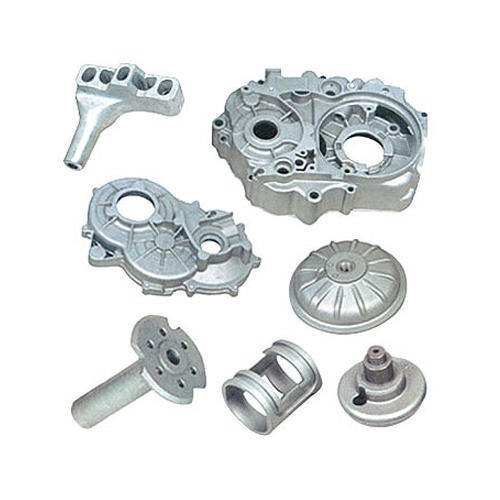
In addition to its precision and flexibility, diecasting also offers notable cost-efficiency advantages, particularly when it comes to production runs with high volumes. Fast cycle times and the minimal waste of materials and a low requirement for labor make it less expensive per unit in comparison to other processes for manufacturing. Furthermore, diecasting molds are durable and can withstand thousands or perhaps millions of cycles, giving excellent returns on investment as time passes. These cost benefits make diecasting an ideal choice for those trying to increase efficiency without compromising on top quality.
In addition, it allows the production of complex and lightweight parts that are crucial for medical equipment and devices. From surgical instruments to implantsable devices the accuracy and reliability of components made by die casting are crucial in ensuring patient safety and efficiency in the medical field. In addition, developments in the field of diecasting, such as vacuum die casting as well as squeeze casting, keep expanding the capabilities that this manufacturing process can provide which allows the manufacture of even more precise as well as high-performance products.